La prevención y el mantenimiento en las fábricas y en la industria en general se ha convertido en un aspecto clave para las empresas. Adelantarse a los problemas parece ser mucho más eficiente y rentable que resolverlos cuando estos suceden. Así lo aseguran los pilares del TPM, una metodología enfocada en el mantenimiento.
¿Quieres saber qué es el TPM, cuáles son los 8 pilares sobre los que se sustenta o cómo ayuda a las empresas que lo ponen en práctica? Descúbrelo a continuación.
¿Qué es el TPM?
El TPM o Total Productive Maintenance (Mantenimiento Productivo Total) es una metodología o estrategia de mantenimiento industrial. Esta trata de afrontar las tareas de mantenimiento de una forma participativa y colectiva, en lugar de dejar este trabajo solamente en mano de los técnicos especializados.
Los 8 pilares de TPM proponen que los trabajadores de las diferentes áreas se impliquen en tareas de mantenimiento diarias. El objetivo es reducir el número de problemas mayores y detectar averías de una manera proactiva. Todo ello contribuye a no detener nunca la producción y mejorar su calidad, así como evitar accidentes de trabajo o reducir el tiempo de las paradas imprevistas.
La dirección de la empresa, junto a ingenieros, mandos medios y técnicos, deben ser los encargados de inculcar los pilares de TPM en la empresa. Esta estrategia tan solo es efectiva si cada uno de los empleados están realmente implicados. Ellos son los últimos responsables de aplicar las tareas de mantenimiento así como de reportar cualquier tipo de problema.
Los 8 pilares del TPM
La metodología y los 8 pilares del TPM tienen su origen en Japón, al igual que algunas metodologías ágiles o el método de las 5S. Esta surgió más concretamente en una filial de componentes electrónicos de Toyota, Nippon Denso Co. donde se decretaron los 8 principios en los que se basa este método de trabajo.
Mejoras Enfocadas o Kobetsu Kaizen
El primero de los 8 pilares del TPM se basa en encontrar oportunidades de mejora a partir de reducir o eliminar desperdicios. Se trata de mejorar continuamente, tratando de llegar a la raíz de los problemas, para crear procesos más eficientes y con menos pérdidas. Permite detectar factores a mejorar y encontrar nuevas soluciones.
Mantenimiento Autónomo o Jishu Hozen
El mantenimiento autónomo está enfocado en que los operarios sean los encargados de aplicar tareas de mantenimiento diarias en los equipos con los que trabajan. Limpieza, orden, inspección, reparaciones menores, etc. Todo ello permite mejorar el funcionamiento de la maquinaria, reducir la rotura de piezas o los accidentes de seguridad.
Mantenimiento Planificado
El tercer pilar de TPM se basa en planificar adecuadamente mantenimiento regulares según las necesidades de cada máquina. El objetivo de esto es reducir a cero las averías, los defectos de fabricación, los despilfarros, los accidentes y la contaminación. Todo ello permite reducir el costo y el tiempo del mantenimiento, así como también eliminar fallos.
Mantenimiento de Calidad o Hinshitsu Hozen
El mantenimiento de calidad consiste en identificar las diferentes causas de los defectos de fabricación. Problemas de maquinaria, de materiales, de metodología, del personal de operaciones… Cualquier detalle puede reducir la calidad de la producción. El objetivo es integrar todos los detalles para solucionar el problema rápidamente.
Prevención del mantenimiento
El quinto de los pilares de TPM consiste en investigar qué nuevas máquinas pueden ser utilizadas para mejorar la producción. Si es necesario se rediseñarán procesos en favor del aumento de la productividad. La integración de la nueva maquinaria se realizará mediante evaluación teórica, test, pruebas FAT y finalmente la puesta en marcha.
Actividades de Departamentos Administrativos y de Apoyo
Los pilares de TPM deben llevarse también a los procesos administrativos, con el objetivo de lograr el equilibrio en todas las áreas de negocio. El objetivo es tratar de mejorar la eficiencia de los procesos administrativos, la gerencia de la empresa o cualquier otra actividad que tenga efecto sobre la producción.
Capacitación y Formación
Otro de los pilares de TPM se basa en la correcta instrucción de los trabajadores. Aumentar los conocimientos de los empleados mediante la capacitación, por ejemplo, permite aumentar el valor de la empresa a largo plazo. Esta debe ser polivalente y de acuerdo con las necesidades tanto de la organización como del empleado.
Gestión de seguridad y Entorno
El último de los pilares de TPM se centra en construir un entorno que reduzca el riesgo de accidente para los operarios. Es imprescindible encontrar soluciones seguras que permitan mejorar los tiempos de producción sin poner en riesgo la salud de los empleados. También se debe tener en cuenta el medioambiente y la contaminación.
Ventajas de aplicar los 8 pilares de TPM
Los pilares de TPM ofrecen un gran número de ventajas a las organizaciones que deciden implementarlo en sus fábricas. Las más destacadas son:
- Reducir el mantenimiento no planificado
- Evitar paradas de producción imprevistas
- Mejorar la calidad de producción
- Reducir los costes de mantenimiento
- Aumentar la eficiencia de los trabajadores
- Evitar que se desaprovechan recursos
- Reducir los accidentes laborales
- Mejorar el rendimiento de los empleados
- Reducir los costos de producción
- Aumentar la rentabilidad
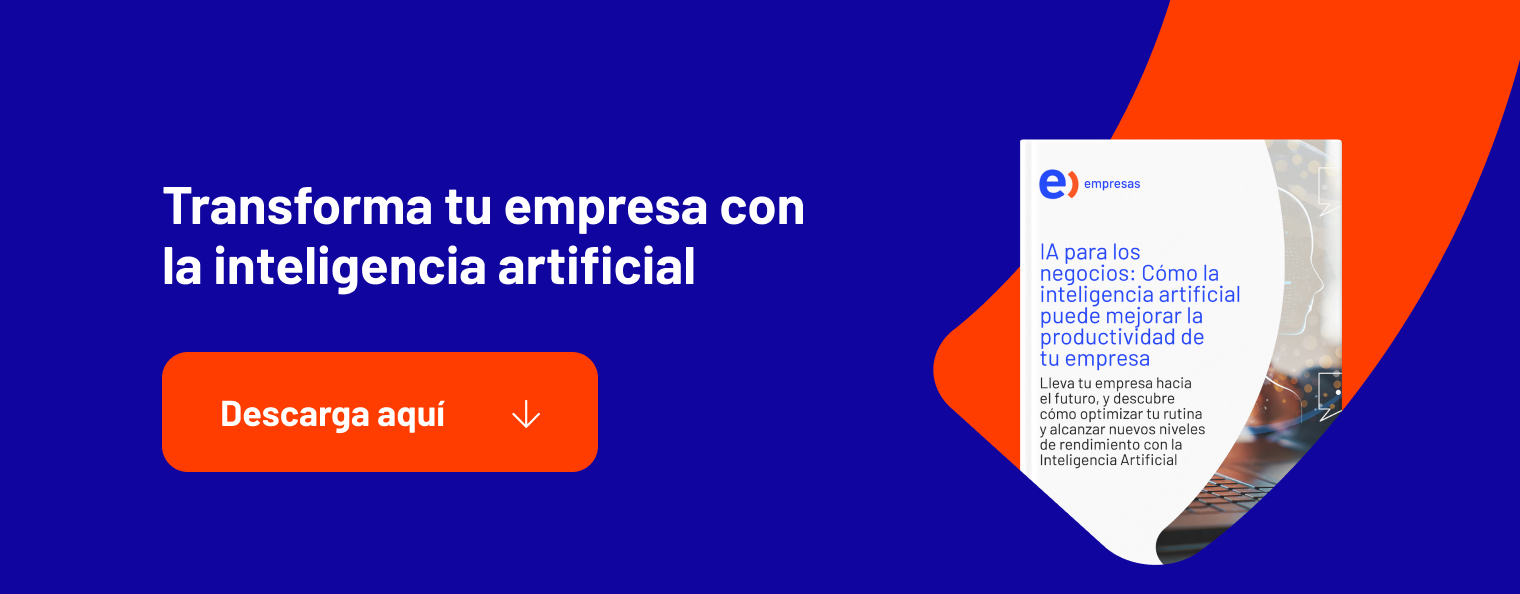